Fensterrahmen vom Bodensee: Da guckt sogar der Kanzler durch
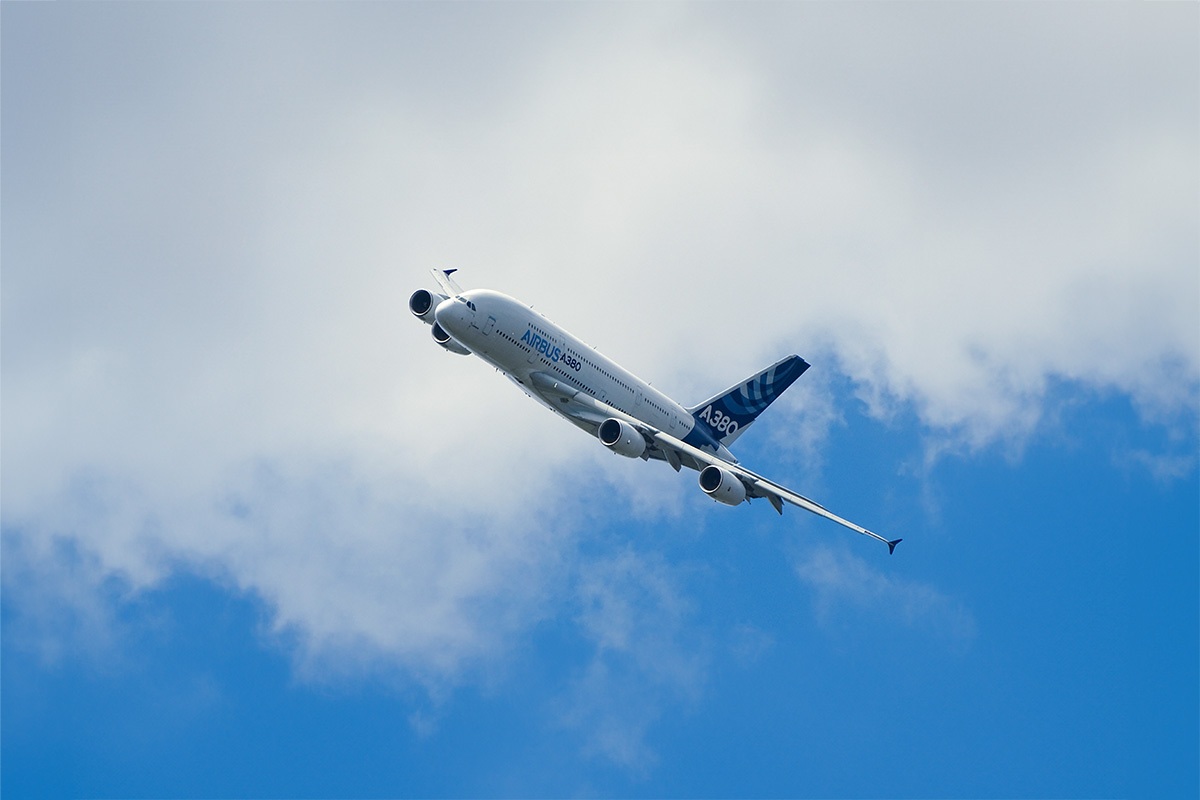
Bodensee: Da guckt sogar der Kanzler durch: Fensterrahmen des Airbus 350 stammen vom Bodensee
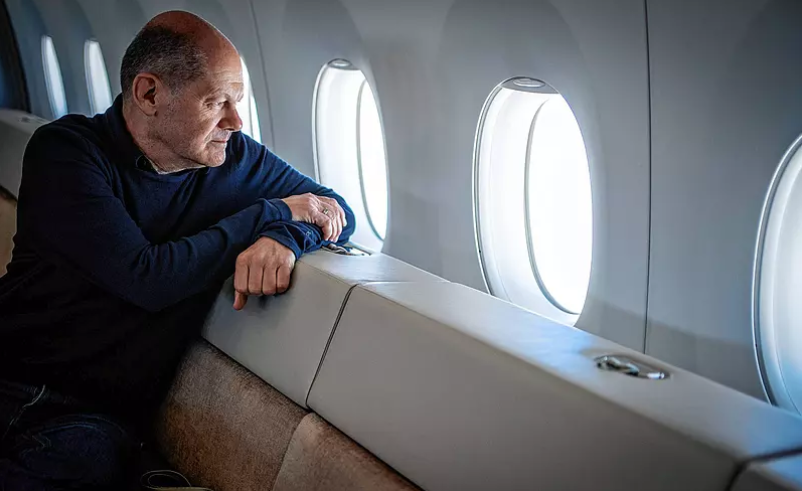
Wer heute in einen Airbus A350 einsteigt, um in den Urlaub zu fliegen oder beruflich zu verreisen, der sieht durch deutlich größere Fenster als früher die Erde entschwinden. Dass das möglich ist, verdankt Airbus der Firma Advanced Composite Engineering (ACE) aus Salem mit zweitem Produktionsstandort in Hagnau. Dort werden die Rahmen beziehungsweise die Flugzeugfenster des Airbus A350 XWB produziert.
Sie bestehen aus carbonfaserverstärktem Kunststoff (CFK), der neben einem großen Gewichtsvorteil gegenüber Stahl oder Aluminium eine hohe Festigkeit und Steifigkeit besitzt. Größere Fenster im Flugzeug, die zum Strukturbauteil des Rumpfes zählen, müssen mehr Belastung als herkömmliche Flugzeugfenster tragen. Das leistet der Fensterrahmen von ACE. Die Firma lieferte bis zur Corona-Pandemie jährlich rund 10.000 Fenster lackiert und vormontiert an Airbus. Rund 30 Prozent ihres Umsatzvolumens erwirtschaftet ACE im Segment Luftfahrt, wesentlich bedeutender ist der Bereich Automotive mit rund 60 Prozent, hinzu kommen zehn Prozent Industrieanwendungen.
Bunte Bauteile von Luxusfahrzeugen
Jürgen Enz, Geschäftsführer von ACE, steht sichtlich stolz im Showroom der Firma in Salem. Dort geht es für den Laien zunächst vor allem bunt zu. An den Wänden hängen grüne, gelbe oder auch rote Bauteile von Luxusfahrzeugen.
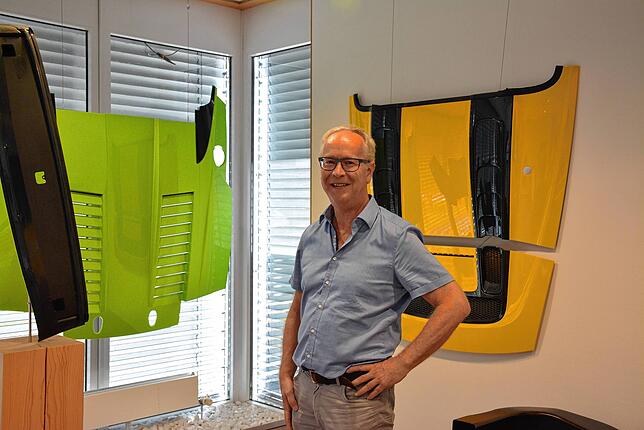
Für den Audi R8 fertigt ACE auch einen Mitteltunnel aus CFK, der von Audi im Rohbau mit Aluminium zusammen eingesetzt wird. Und wieso nicht ganz aus Kohlefaser? „Kohlefaser ist teurer als Aluminium“, sagt Jürgen Enz. Aufrecht steht daneben unter anderem ein rund zwei Meter langes röhrenartiges schwarzes Gebilde. Es handelt sich um das Carbon-Gelenkwellengehäuse, das den Motor mit dem Getriebe strukturell verbindet. Jürgen Enz: „In Aluminium wiegt das Bauteil 27 Kilo, in CFK nur 13 Kilo.“
Viel leichter als Aluminium
Das geringe Gewicht ist ein wesentlicher Grund, wieso Automobilhersteller, aber auch die Luftfahrtindustrie, Bauteile aus Kohlenfaserstoff einsetzen. Es geht neben der Festigkeit und Steifigkeit vor allem um das Gewicht der Fahr- beziehungsweise Flugzeuge. Durch den Einsatz von CFK kann es deutlich verringert werden. Zum Beispiel beim BMW i8, dem elektrisch getriebenen Sportwagen der Münchner Autobauer. Um das Fahrzeug besonders leicht zu bauen, ließ BMW von ACE die ganze Seitenwand in CFK erstellen. „BMW setzt auch weiter auf Kohlefaser“, erklärt Jürgen Enz, der aber weiß, dass der Nachfolger des i3 aus einer Mischbauweise CFK/Aluminium bestehen wird. Mischbauweisen sind nicht unüblich. So besteht beispielsweise die Rohbauplattform des Audi R8, die der vom Lamborghini Huracán entspricht, aus Aluminium und CFK. Auch an ihr wirkt ACE mit.
Die Dienstleistungspalette von ACE reicht von der Konzeption, der Konstruktion und Dimensionierung eines Bauteils bis hin zur Produktion von Prototypen und Serien. Dabei nutzten die Salemer das sogenannte RTM-Verfahren. RTM steht für Resin Transfer Moulding und bedeutet, dass trockene Fasern, wie zum Beispiel Kohlenstofffasern, oder vorgefertigte Preformlinge in ein Werkzeug eingelegt werden und dann, nach dem Schließen der Form, flüssiges Harz unter hohem Druck in die geschlossene Form injiziert wird. „Wir realisieren Leichtbaustrukturen von der Entwicklung bis zur Serie“, heißt es auf der Website des Unternehmens.
So produziert ACE beispielsweise diverse Abdeckungen für hochmotorisierte Fahrzeuge – womit man wieder im Showroom von ACE angekommen wäre. Hier findet sich unter anderem die Motorklappe aus Kohlefaser für den Coupe des Aventador von Lamborghini. Zehn Jahre lang produzierte ACE das Bauteil, doch jetzt stellt die VW-Tochter Lamborghini den Aventador ein. „Serienende ist in diesem Monat“, sagt Jürgen Enz, doch das bedeute nicht das Aus für ACE. „Auch bei dem Nachfolger des Aventador werden wir mit dabei sein“, sagt er.
Boxen für Batterien sind in Arbeit
Der Ingenieur sieht der Veränderung des Automobilmarktes gelassen entgegen. Schon heute arbeite man an Boxen für Batterien mit. Sie müssten nicht nur leicht, sondern vor allem auch den auf sie wirkenden Kräften entsprechend fest sein. „Sie müssen einen Crashtest überstehen“, weiß Jürgen Enz, da käme der Faserverbund wieder ins Spiel. Schwere Lastwagen oder Flugzeuge könnten zudem nicht batteriebetrieben unterwegs sein, hier komme dem Wasserstoff und der Brennstoffzelle eine entscheidende Rolle zu. Bei der Herstellung der benötigten Drucktanks sei die Kohlefaser schon heute gesetzt.