Window frames from Lake Constance: Even the chancellor looks through them
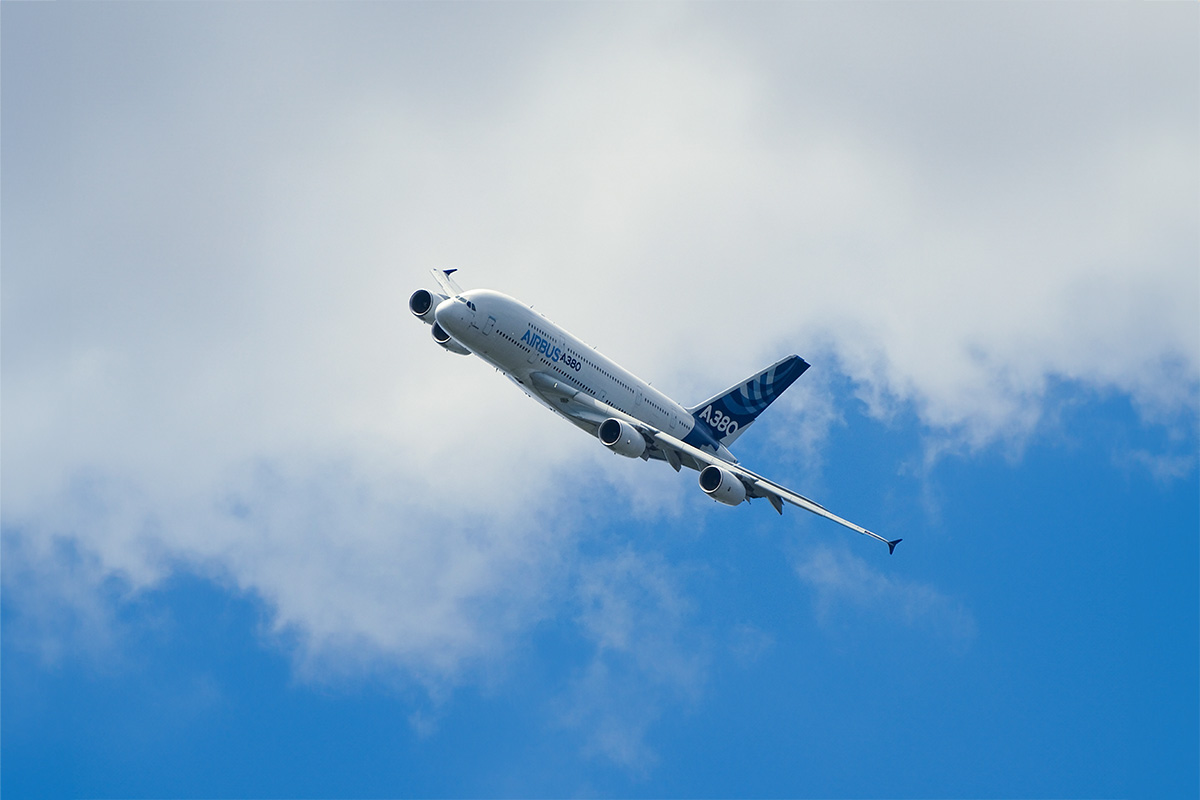
Lake Constance: Even the Chancellor is looking through it: Airbus 350 window frames come from Lake Constance
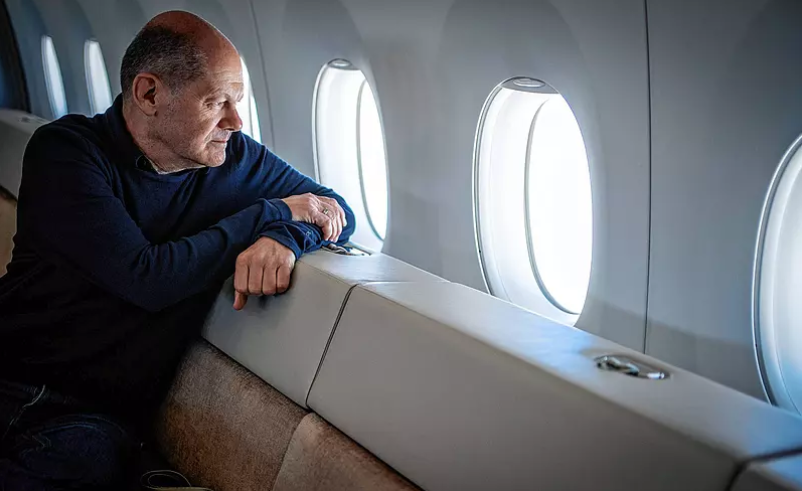
Anyone who boards an Airbus A350 today to fly on vacation or travel for work sees the earth disappearing through significantly larger windows than before. Airbus owes that this is possible to Advanced Composite Engineering (ACE) from Salem with a second production site in Hagnau. The frames and aircraft windows of the Airbus A350 XWB are produced there.
They consist of carbon fiber reinforced plastic (CFRP), which, in addition to a major weight advantage over steel or aluminum, has high strength and stiffness. Larger windows in aircraft, which are part of the structural part of the fuselage, must bear more load than conventional aircraft windows. The ACE window frame does that. Until the corona pandemic, the company delivered around 10,000 painted and pre-assembled windows to Airbus. ACE generates around 30 percent of its sales volume in the aviation segment, the automotive sector is much more important with around 60 percent, plus ten percent industrial applications.
Colourful components of luxury vehicles
Jürgen Enz, managing director of ACE, is visibly proud in the company's showroom in Salem. For the layman, it's primarily colorful at first. Green, yellow or even red luxury vehicle components hang on the walls.
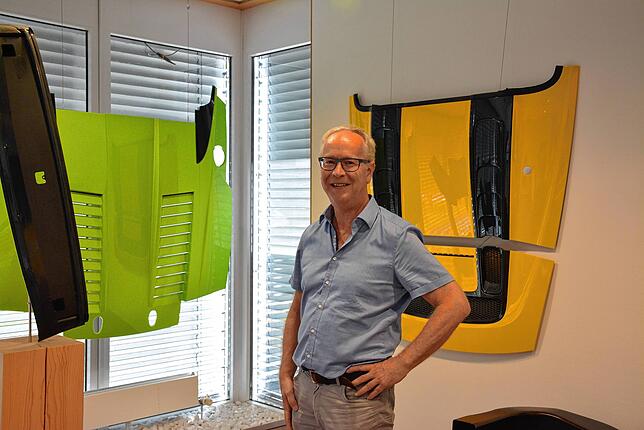
For the Audi R8, ACE also produces a central tunnel made of CFRP, which Audi uses together with aluminum in the shell. And why not make entirely of carbon fiber? “Carbon fiber is more expensive than aluminum,” says Jürgen Enz. Among other things, a tubular black structure around two meters long stands upright. It is the carbon cardan shaft housing, which structurally connects the engine to the transmission. Jürgen Enz: “In aluminum, the component weighs 27 kilos, in CFRP only 13 kilos. ”
Much lighter than aluminum
The low weight is a major reason why automotive manufacturers, but also the aviation industry, use carbon-fiber components. In addition to strength and stiffness, it is primarily about the weight of vehicles and airplanes. By using CFRP, it can be significantly reduced. For example with the BMW i8, the electric-powered sports car from Munich-based car manufacturers. In order to make the vehicle particularly lightweight, BMW Create the entire sidewall from ACE in CFRP. “BMW continues to rely on carbon fiber,” explains Jürgen Enz, who knows, however, that the successor to the i3 will consist of a CFRP/aluminum composite construction. Mixed construction methods are not uncommon. For example, the body shell of the Audi R8, which is the same as that of the Lamborghini Huracán, is made of aluminum and CFRP. ACE is also involved in it.
ACE's range of services ranges from the design, construction and dimensioning of a component to the production of prototypes and series. The people of Salem used the so-called RTM process. RTM stands for resin transfer molding and means that dry fibers, such as carbon fibers, or preformed preforms are inserted into a tool and then, after closing the mold, liquid resin is injected into the closed mold under high pressure. “We implement lightweight structures from development to series production,” says the company's website.
ACE, for example, produces various covers for highly motorized vehicles — which would have brought you back to the ACE showroom. This includes the carbon fiber engine flap for the Lamborghini Aventador coupe. ACE produced the component for ten years, but now VW subsidiary Lamborghini is discontinuing the Aventador. “The end of the series is this month,” says Jürgen Enz, but that doesn't mean the end for ACE. “We will also be involved in the successor to the Aventador,” he says.
Boxes for batteries are in progress
The engineer looks forward calmly to the change in the automotive market. They are already working on boxes for batteries. They must not only be lightweight, but above all strong according to the forces acting on them. “They have to survive a crash test,” says Jürgen Enz, that's where the fiber composite comes back into play. In addition, heavy trucks or airplanes could not be battery-powered; hydrogen and fuel cells play a decisive role here. Carbon fiber is already being used today to manufacture the required pressure tanks.